In an industry such as laundry, operational efficiency is critical to the success of your business. Speed and precision are crucial in this industry, being the driving force for optimal productivity, impeccable cleanliness and overall success. Whether you run a small neighbourhood laundry or a large-scale commercial laundry service, operational efficiency is non-negotiable.
The process of optimising your laundry operations into a smooth and error-free workflow can turn your laundry business into an impeccable force. Some of the benefits include:
- Time savings: efficient operations can save significant time, which can be invested in other areas of the business such as strategic planning. Every minute saved is a minute gained in the laundry business!
- Service improvement: A smooth workflow reduces the possibility of errors and improves the quality standard of service. In the world of laundry, service quality is measured by the cleanliness of the laundry you deliver. If you can offer a consistently superior service, you will build an unsurpassed reputation.
- Increased customer satisfaction: By delivering perfectly clean and folded clothes every time, you will exceed your customers' expectations, thus enhancing their satisfaction and loyalty.
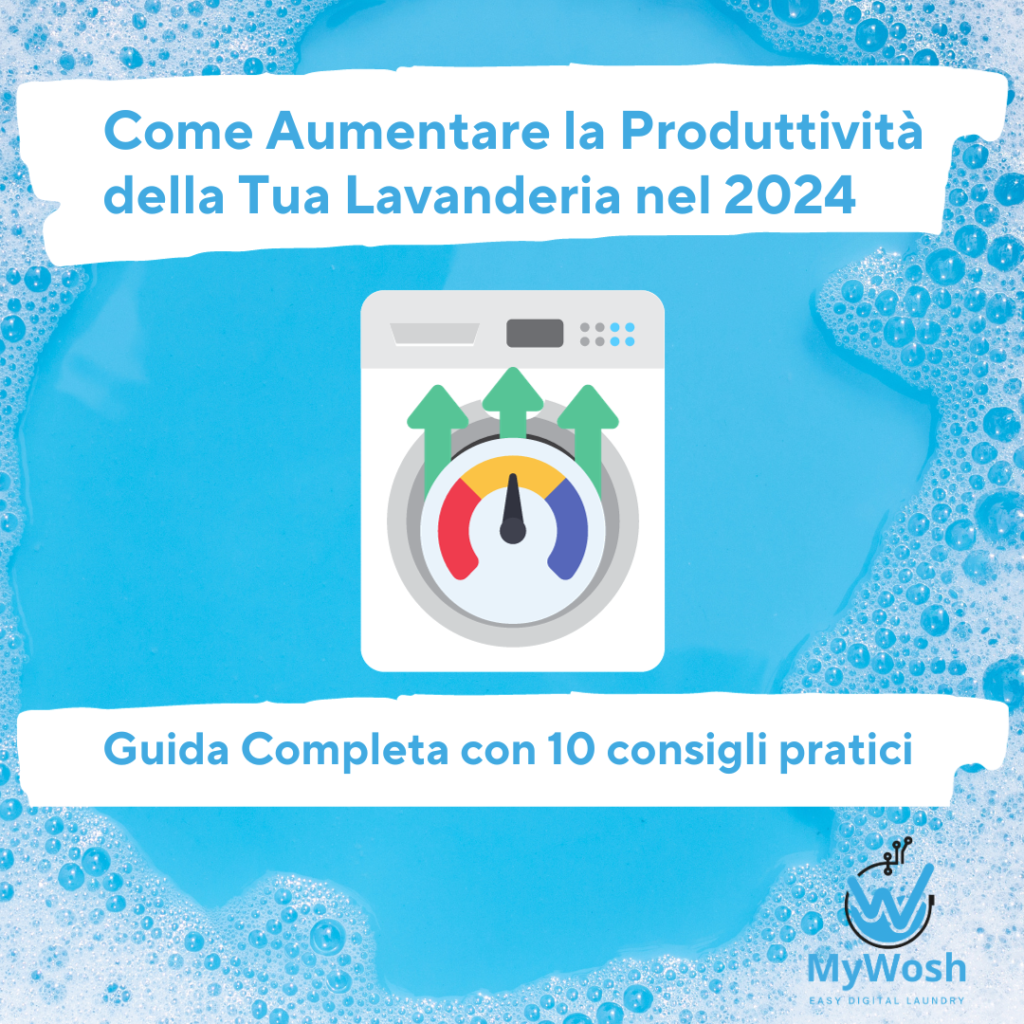
Achieving these high levels of efficiency takes hard work, but perhaps more importantly, it requires a deep commitment to the laundry process, continuous training and modern tools. Read on to find out everything you need to know about making laundry operations more efficient and how digital tools can help you take your business to the next level.
Laundry Operations
Impeccably cleaning a wide range of fabrics and materials is central to laundry operations. This is true in numerous contexts, from hospitality and healthcare to commercial laundries and residential environments.
In thehospitality industry, such as hotels and resorts, laundry operations ensure that guests have a constant supply of fresh, clean linen. This contributes significantly to the guest experience and overall satisfaction.
In the health sector, effective laundry operations help maintain the cleanliness and hygiene of sheets and uniforms, playing an instrumental role in infection control, so that all fabrics used are safe and free of bacteria or viruses.
At commercial settings, laundry operations serve businesses such as self-service laundries and industrial laundries that provide laundry services to various customers, including hospitals, hotels, restaurants and other businesses.
In residential setting, laundry operations boil down to the process each household goes through to keep its clothes and textiles clean and fresh.
Regardless of the context, the key components of laundry operations are generally the same:
- Selection: Garments are categorised according to colour, type of fabric and level of soiling. Correct sorting can prevent colour spillage, damage to delicate fabrics and result in a more effective cleaning process.
- Washing: Garments are cleaned using a washing machine or by hand, depending on the fabric and care instructions. This process involves the use of detergents and water to remove dirt and stains.
- Drying: After washing, the clothes are dried in a tumble dryer or in the air. Special care is taken to follow the drying instructions on the clothes to avoid shrinkage or damage to the fabric.
- Folding or Ironing: Once dry, the clothes are folded or ironed to give them a tidy appearance. For commercial operations, this stage often also includes wrapping and preparing items for delivery or collection.
During these steps, laundry operations can encounter several challenges. Stain removal is a common problem, with different stains requiring specific treatments. Understanding how to effectively treat a wide range of stains is crucial to ensure fabric quality every time.
Caring for garments is another challenge that requires knowledge and experience. Not all garments are the same: they are made of different fabrics and colours, each with its own care instructions. For example, silk should not be washed with normal detergent or subjected to intense spin cycles. Instead, it should be hand-washed with a mild soap and gently blotted with a towel to remove excess water, or better still, dry-cleaned.
Wool is another difficult fabric that requires special care. It can shrink or warp when washed in hot water or dried in a washing machine. This fibre should be washed by hand in cold water with a detergent specially designed for wool and laid flat to dry. Ignoring these instructions can lead to damage, loss of colour, changes in size and shape of the garment and dissatisfied customers.
Indispensable Tools and Equipment for Operational Success
Efficient laundry operations require specialised equipment and high-quality cleaning products to ensure consistently good results. Whether you are serving residential, commercial or institutional customers, these are some of the tools and equipment you need to equip your laundry.
- Commercial Washing Machines: The cornerstone of any laundry operation, commercial washing machines come in a variety of models and sizes. They are typically larger than residential washing machines, designed to handle a significant volume of laundry and run continuously. Their advanced features often include programmable settings that allow customised cycles based on fabric type and soil level, ensuring thorough cleaning without damaging fibres
- Dryers: After washing, the next critical piece of equipment is the commercial dryer. Like their washing counterparts, commercial dryers are designed to handle high volume loads and dry them efficiently. Many models are equipped with features such as humidity sensors and heat settings to ensure that all items are dried thoroughly without over-drying, which could cause shrinkage or fabric damage.
- Ironing Systems: In many operations, especially in the hospitality and commercial sectors, an industrial ironing system is a necessity. These systems ensure that sheets, uniforms and other textiles are ironed crisply and wrinkle-free, presenting a clean, professional appearance. More complex systems are capable not only of ironing, but also of folding and stacking items
In addition to this central equipment, laundry operations also require a range of professional cleaning products in order to achieve the end result that customers are looking for.
• Detergents: The right detergent can make a considerable difference in the final product. Commercial detergents are formulated to tackle stubborn stains in high volume laundry loads. When choosing a detergent, consider factors such as the hardness of the water in your area and the types of fabric you usually wash.
• Softeners: These are used to keep fabrics soft, reduce static and give the garment a fresh smell. Make sure you choose a fabric softener that is compatible with the content of your wash load and the type of washing machine.
• Whiteners: For those tougher stains that normal detergents cannot fully treat, whitener comes into play. Keep in mind that different bleaches are designed to target specific types of stains, so having a variety of bleaches on hand can be a smart move.
Maintaining and troubleshooting your equipment is another important aspect of efficient operations. In a perfect world, nothing ever goes wrong, wear and tear does not exist, and your equipment always works at its best! But realistically, you should perform regular inspections and maintenance to prevent build-up and blockages. Watch out for unusual noises or reduced performance, which could indicate the need for repairs or parts replacement. A little basic knowledge in troubleshooting common problems can save downtime and costs associated with technician visits.
Optimise Laundry Processes to Increase Productivity
Once you have mastered the basic concepts, you can incorporate digital tools, advanced systems and data analysis into your laundry operations. By harnessing modern technology in your laundry operations, you can make targeted interventions in your processes, correct inefficiencies otherwise ignored, maximise margins and gain an edge over your local competitors.
Implement an Enterprise Management System for Laundry
Historically, laundry operations have been manual, time-consuming and error-prone. One of the most transformative tools for streamlining laundry operations today is a laundry management system. By introducing a robust software solution such as MyWosh into your laundry operations, you can significantly increase the efficiency and productivity of your business.
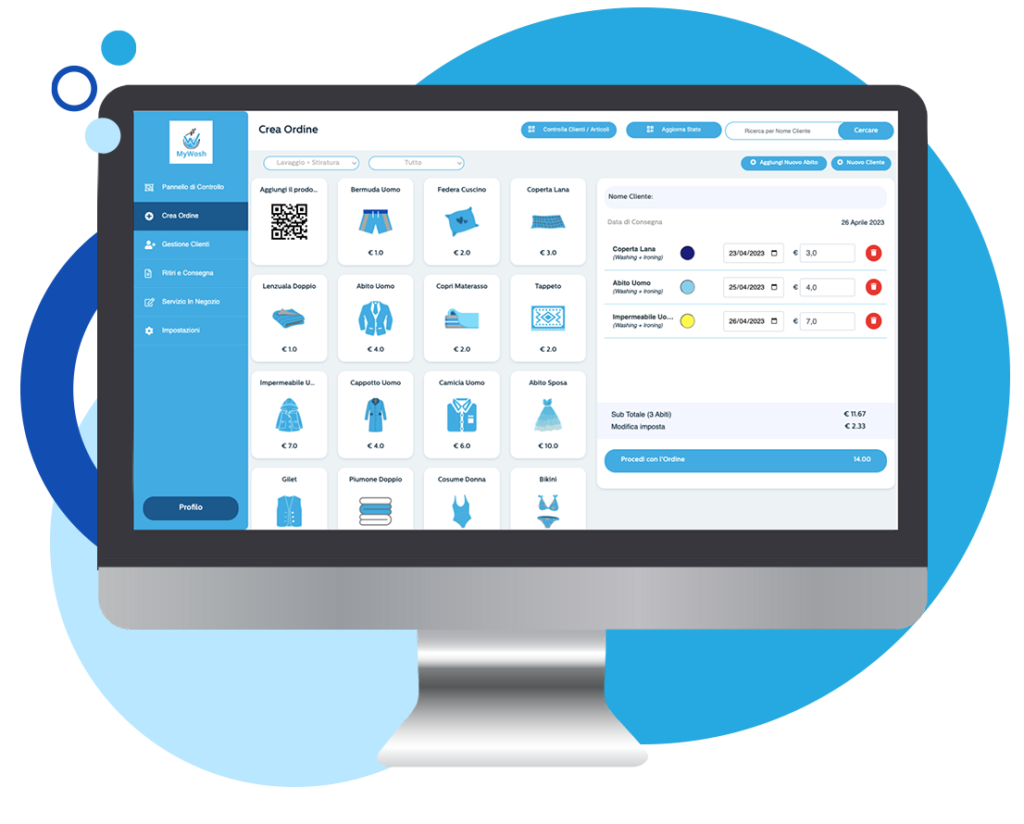
What makes a laundry management system special is its ability to automate numerous tasks that would otherwise be manual and time-consuming. The result? Owners and operators can devote their valuable time and energy to growth-enhancing tasks, such as customer service and strategic planning, instead of mundane tasks.
Key features of the laundry management software include comprehensive inventory management, advanced planning capabilities and robust reporting functions:
- Inventory Management: Through a digital platform, you can monitor the use of cleaning products and equipment, identify trends and make informed decisions on when to restock. This prevents unplanned shortages and helps you avoid unnecessary expenses due to overstocking.
- Planning: With a laundry management system, operators can easily plan tasks, assign responsibilities to employees and monitor the progress of each operation. This enables a smooth workflow, ensuring that no step is overlooked or delayed.
- Reporting: Reporting is a valuable, but often overlooked, aspect of any laundry operation. With laundry management software, operators gain direct visibility into business performance, such as operating costs, productivity rates and revenues. This data can be used to make strategic decisions and identify areas for improvement.
Another great advantage of a laundry management system is its ability to simplify complex tasks:
- Order Tracking: Managing orders can be an overwhelming task, especially for larger operations. With a laundry management system, orders can be easily tracked, monitored and managed digitally, increasing efficiency and customer satisfaction.
- Customer Communication: Maintaining clear and consistent communication with customers is of utmost importance. Through automated notifications, updates and reminders, a laundry management system maintains a constant line of contact with your customers, so that they never feel left out about the status of their laundry.
- Invoicing: Calculating costs, creating invoices and processing payments can be time-consuming. A laundry management system automates these processes, making them faster, easier and more accurate.
The benefits of implementing a laundry management system are manifold, from increased operational efficiency to increased customer satisfaction. It is a sound investment that can take laundry operations to a higher level of productivity and success.
Optimise Workflows with Technology
In an industry as outdated as the laundry industry, harnessing the power of technology can help you streamline your workflow and push yourself to the forefront. With the right innovative tools, you will be able to greatly simplify laundry processes, improve efficiency and reduce the need for manual labour, all with just a few clicks.
An example of this is the QR code identification systems. These systems allow efficient tracking and sorting of garments, facilitating inventory and order management. Here is how they work:
- Each garment has a unique QR-code that contains information about the garment, such as type, material, owner, cleaning instructions.
- Marked items can then be quickly scanned and sorted, saving considerable time and reducing the risk of human error.
Another significant technological advance that has proved beneficial in the laundry industry is the integration of automation tools such as belt conveyor systems or robotic assistance.
- Conveyor Belt Systems: Automated belt conveyor systems can transport large volumes of laundry from one process to another, eliminating the need for manual handling and reducing the risk of workplace injuries. They also speed up the entire laundry process, increasing operational efficiency.
- Robotics Assistance: Robotic technologies can assist in tasks such as folding or sorting laundry, again reducing manual labour and increasing efficiency. They work around the clock, improving productivity and delivering consistent performance. Imagine doing laundry while you sleep!
Intelligent machines are another technology that is revolutionising the way laundry operations work. Modern commercial washing machines and dryers often feature programmable cycles that allow customisation to the specific needs of each load. This paves the way for optimal cleaning results while preserving the life of fabrics and the efficiency of equipment and products. These intelligent machines also offer remote monitoring capabilities. Managers can check machine status, troubleshoot problems and even change settings from anywhere, using a smartphone or computer.
This level of control and flexibility significantly improves the efficiency of the laundry process. By investing in these solutions, you can boost productivity, reduce operating costs and deliver better results to your customers.
Make Strategic Decisions Based on Data
Data analysis is the secret to optimising laundry operations. With the help of advanced tools like MyWosh, laundry owners can now collect, analyse and interpret data to improve inefficiencies that escape the naked eye.
The role of data analysis in the optimisation of laundry processes
Every aspect of the laundry process, from the registration of the customer's order to its completion, generates valuable data. Analysis is the process of finding meaning in this data and using it to improve operations and capitalise on your strongest revenue generators. For example, data on the time taken to process different types of orders can help identify inefficiencies and areas for process optimisation.
MyWosh is designed to capture and analyse these key metrics, providing valuable insights for decision-making. By automating data collection and analysis, MyWosh simplifies the task of laundry owners in identifying and addressing inefficiencies.
Data-driven insights enable laundry owners to make informed decisions. By identifying critical points in the laundry process, resources can be allocated more efficiently, leading to improved productivity and increased profits. For example, if data reveal that a specific step in the cleaning process consistently causes delays, strategies can be devised to make that step more efficient. Data analysis also makes it easier to detect trends. This could mean identifying the busiest days of the week, understanding which services are most popular or even discerning customer preferences for delivery or collection times.
MyWosh uses advanced algorithms to detect trends and patterns, providing practical insights that can guide promotional activities, personnel adjustments and operational strategies.
Prioritise Training and Employee Adoption
The effectiveness of a digital solution like MyWosh is only as good as its adoption rate. To realise its full potential, companies must ensure that employees are competent with the new system and able to navigate it effortlessly. This is why training and employee adoption are crucial aspects of implementing a laundry management system.
Importance of comprehensive employee training
Employee training is the fuel for a successful technology implementation. Spend time to ensure that employees are comfortable with the new system, understand its functionality and can use it to its full potential. From using the management system to generating reports and troubleshooting, employees should be equipped with the necessary skills to operate the laundry management software efficiently. Remember, training should not be a one-off process, but rather an ongoing activity that keeps employees up-to-date with new features and updates.
Empowering staff through digital competence
Empowering staff to navigate digital tools is crucial in today's technology-driven world. Digital competence not only improves efficiency, but also opens up avenues for innovation and problem solving. With the right support, employees can maximise the potential of a laundry management system like MyWosh, leading to improved operational efficiency and superior customer service.
Digital skills also increase employee engagement. Employees who feel comfortable using technology are more likely to be engaged in their work. They feel empowered and valued, which can lead to greater job satisfaction and retention.
Do not underestimate the power of effective change management
Change, although necessary, can often be met with resistance. Here are some tips for managing this transition smoothly:
- Clear Communication: From the outset, communicate the reason behind the implementation of the new system, the benefits it will bring to employees and the company as a whole. The new software will make life easier for team members by reducing boredom. Open and transparent communication reduces uncertainty and fosters a culture of acceptance.
- Continuous SupportOffer continuous support to employees during the transition phase. This might involve offering additional training sessions, appointing leaders to help others or setting up a helpdesk to address questions and concerns.
- Feedback Channels: Establish clear channels for employees to express feedback and concerns about the new system. Employees who feel listened to are more likely to accept the change and adopt the new system. Their feedback could also provide valuable information to improve the system and make it more user-friendly.
- Patience and Encouragement: Understand that mastering a new system takes time. Encourage employees and appreciate their efforts during the transition. Patience and positivity can contribute to a smooth transition.
The successful implementation of a laundry management system like MyWosh depends on the adherence of employees and how well they are trained. With comprehensive training and effective change management, you can facilitate a smooth transition, resulting in increased productivity, superior service and, ultimately, a prosperous company.
Keep Improving and Adapting
The laundry industry is dynamic and constantly evolving. To remain competitive, companies must constantly strive to improve their operations and adapt to inevitable changes. Implement a management system like MyWosh is not an occasional activity, but rather a path of continuous improvement and adaptability.
Embrace a culture of continuous improvement
Continuous improvement means perpetually looking for ways to improve operations and enhance customer experiences. For laundry owners, this might involve constantly analysing the data collected by the MyWosh platform, trying to understand how existing processes can be improved or exploring new ways to offer better service to customers.
Periodically review processes and implement feedback
To promote continuous improvement, regular reviews of processes and operations are essential. It is important to analyse key performance indicators (KPIs) and customer feedback to identify areas requiring improvement or change. Similarly, actively seeking and implementing feedback from employees on the front end can lead to substantial improvements.
Keeping up with technology and trends
The digital world is moving fast, and in order to keep up, business owners need to stay abreast of new emerging technologies and industry trends. For laundries, this might mean keeping an eye on developments in laundry technology, eco-friendly practices, new marketing strategies or evolutions in customer expectations.
The New Era of Optimised Laundry Operations
The digital transformation of the laundry industry, embodied in advanced systems like MyWosh, has ushered in a new era of optimised laundry processes and efficiency. One of the greatest benefits of incorporating technology is the automation of manual and time-consuming tasks.
Not only does this reduce opportunities for human error, it also allows owners and operators to focus on the core aspects of their business, such as strategic planning and enhanced customer service. The ability to monitor key performance metrics and analyse data provides insight into your operations, uncovering insights that can lead to improved workflows and greater efficiency.
Adopting a laundry management system like MyWosh is an investment that yields considerable returns in the long run It's time to harness the power of technology and transform your traditional laundry into a digital, data-driven business. Embrace these digital solutions, optimize your workflows, improve efficiency and watch as your productivity reaches new heights! on data.